Table of Contents
Toggle- What Are Motor Starters?
- How Motor Starters Work
- Types of Motor Starters
- Choosing the Right Motor Starter
- The Role of Motor Starters in Industrial Applications
- Key Functions of Motor Starters in Industrial Environments
- The Importance of Bench Testing Before Installation
- How to Bench Test a Motor Starter
- Conclusion
Motor starters are essential components in industrial and commercial electrical systems, ensuring the safe and efficient operation of electric motors. Whether it’s a manufacturing plant, a facility management system, or a contractor working on a large-scale project, selecting the right motor starter can significantly impact efficiency, energy savings, and equipment lifespan.
In this comprehensive guide, we will cover everything you need to know about motor starters—including their types, how they work, and why they are crucial for industrial applications.
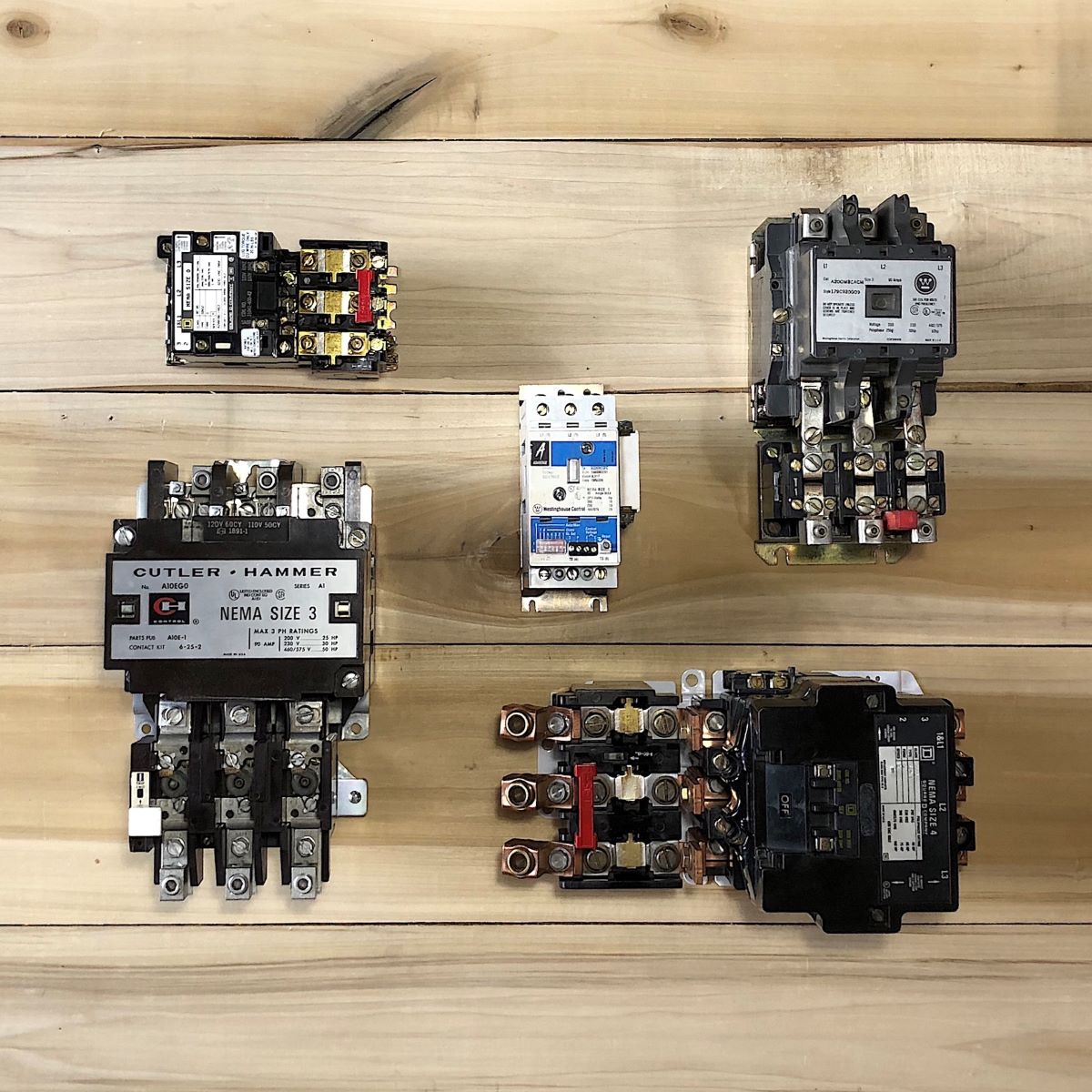
What Are Motor Starters?
In industrial and commercial settings, electric motors power essential machinery and equipment. However, directly supplying power to a motor without regulation can cause excessive electrical surges, leading to mechanical stress, overheating, and even system failures. This is where motor starters come in.
A motor starter is an electrical device designed to safely start, stop, and protect an electric motor. It controls the electrical current flow, ensuring that motors receive the right amount of power without damaging components or causing electrical hazards. Motor starters go beyond just turning motors on and off; they also incorporate protective mechanisms like overload protection, short-circuit prevention, and phase failure detection to prevent damage and enhance workplace safety.
Motor starters are widely used in industries such as manufacturing, automation, HVAC, and electrical contracting, where smooth and controlled motor operation is critical. By properly regulating the power supply, motor starters contribute to increased energy efficiency, prolonged motor lifespan, and reduced downtime—all essential factors for cost-effective industrial operations.
Next, let’s explore how motor starters work.
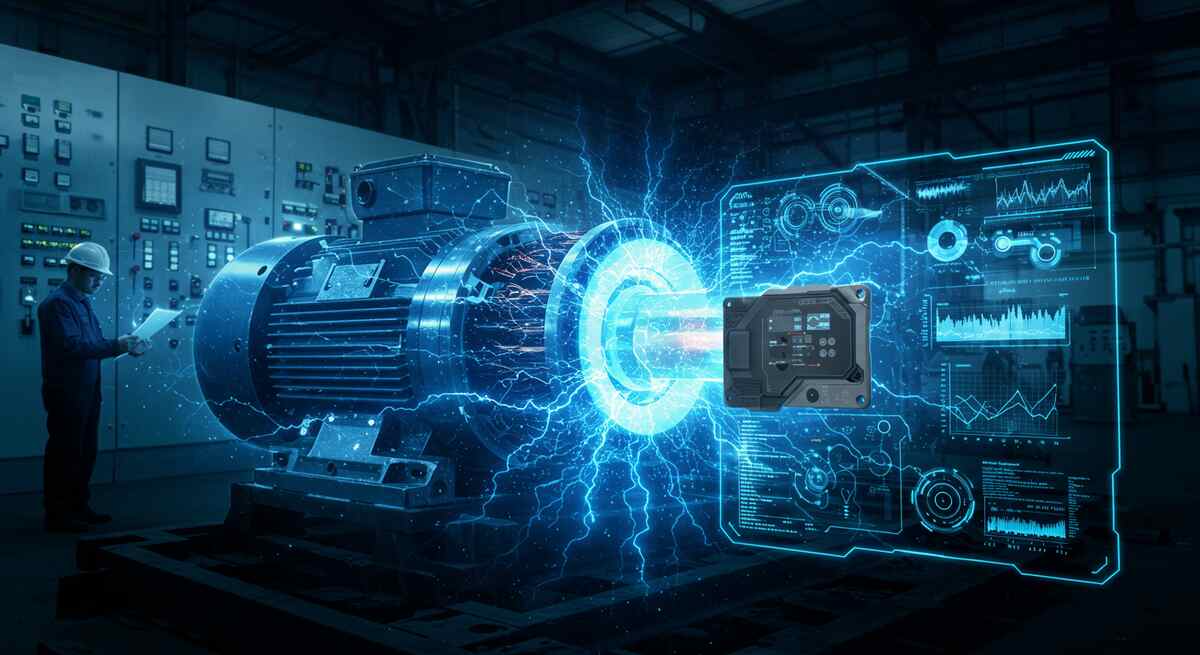
How Motor Starters Work
Understanding how motor starters operate is essential for electrical contractors, system integrators, and facility managers who rely on industrial motor control. These devices function as a bridge between the power supply and the motor, ensuring a safe and controlled start-up while protecting against potential hazards.
Key Components of a Motor Starter
Motor starters typically consist of two main components:
- Contactor: This is an electrically controlled switch that opens or closes the circuit to either start or stop the motor. The contactor handles high currents safely, preventing electrical damage.
- Overload Relay: This component monitors the current drawn by the motor. If the motor exceeds its rated current due to excessive load or system failure, the overload relay trips, cutting off power to prevent overheating and potential motor damage.
Step-by-Step Operation of a Motor Starter
- Initiation: When a motor starter is activated, the contactor closes, allowing electrical current to flow from the power source to the motor.
- Power Regulation: The starter ensures a smooth transfer of power, preventing sudden voltage spikes that can stress the motor.
- Continuous Monitoring: The overload relay continuously checks the current level. If an abnormal surge or prolonged overload occurs, it interrupts the power supply to prevent overheating.
- Shutdown & Protection: If an issue such as phase failure or an overload is detected, the motor starter trips, shutting down the motor to avoid system damage.
Why Is This Process Important?
- Prevents Electrical Damage: Limits inrush current to avoid burning out the motor.
- Enhances Safety: Protects against electrical faults, reducing fire and shock hazards.
- Increases Efficiency: Ensures that motors operate optimally without excessive energy consumption.
Now that we understand how motor starters work, let’s look at the different types of motor starters and their applications.
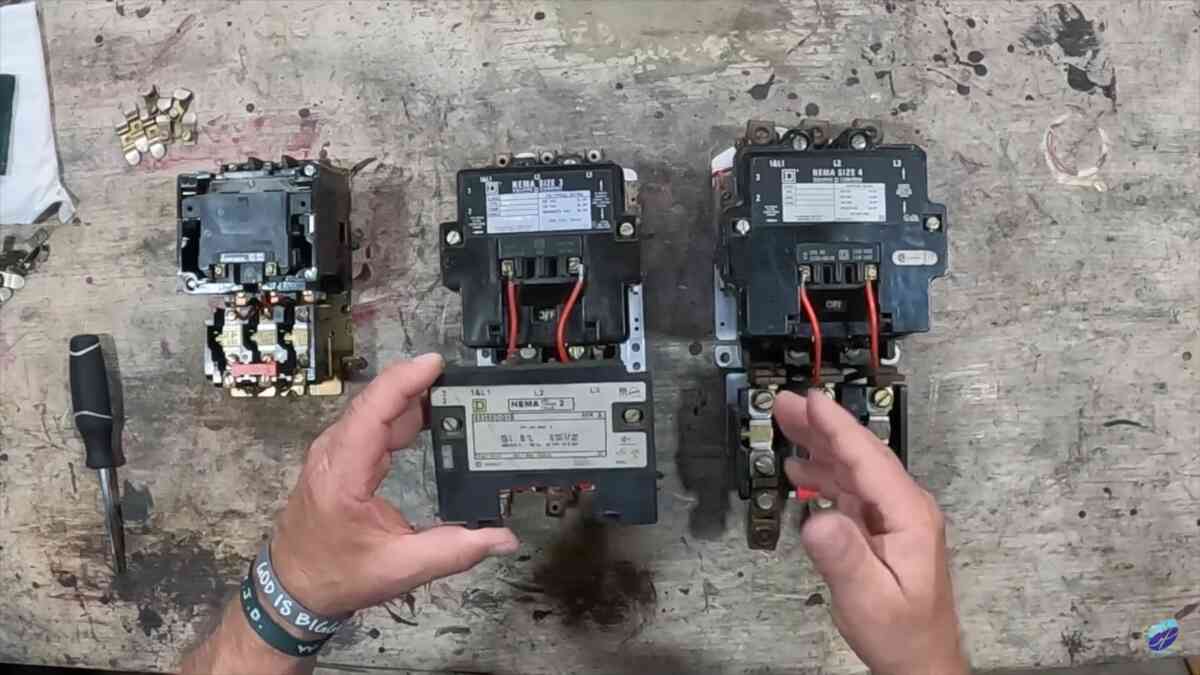
Types of Motor Starters
Motor starters come in various types, each suited to different applications based on motor size, power requirements, and operational needs. Selecting the right motor starter is crucial for ensuring efficient motor performance, minimizing energy waste, and protecting electrical systems.
Direct-On-Line (DOL) Starters
Best for: Small motors with low starting current requirements.
- How it works: Connects the motor directly to the power supply, providing full voltage instantly.
- Advantages: Simple, cost-effective, and easy to install.
- Limitations: Causes a high inrush current, which may stress larger motors.
Common Applications:
- Small pumps and compressors
- Fans and conveyors
- Simple automation systems
Star-Delta Starters
Best for: Medium to large motors that require reduced starting current.
- How it works: Initially starts the motor in a star configuration, reducing voltage and current draw. Once the motor reaches sufficient speed, it switches to a delta configuration for full operation.
- Advantages: Reduces the initial surge of current, minimizing stress on electrical components.
- Limitations: Requires additional wiring and control systems.
Common Applications:
- Large pumps and air compressors
- Industrial HVAC systems
- Conveyor belts with heavy loads
Soft Starters
Best for: Applications where smooth acceleration and deceleration are necessary.
- How it works: Uses electronic circuits to gradually increase voltage, allowing for a smooth motor start.
- Advantages: Reduces mechanical stress and extends motor lifespan.
- Limitations: Higher initial cost compared to traditional starters.
Common Applications:
- Heavy-duty machinery
- Water pumps and irrigation systems
- Material handling systems
Manual Motor Starters
Best for: Small applications requiring direct manual control.
- How it works: Uses a physical switch to start and stop the motor while providing basic overload protection.
- Advantages: Simple and inexpensive.
- Limitations: Requires manual intervention, not suitable for automated systems.
Common Applications:
- Small workshop equipment
- Simple fan or pump systems
- Emergency motor control situations
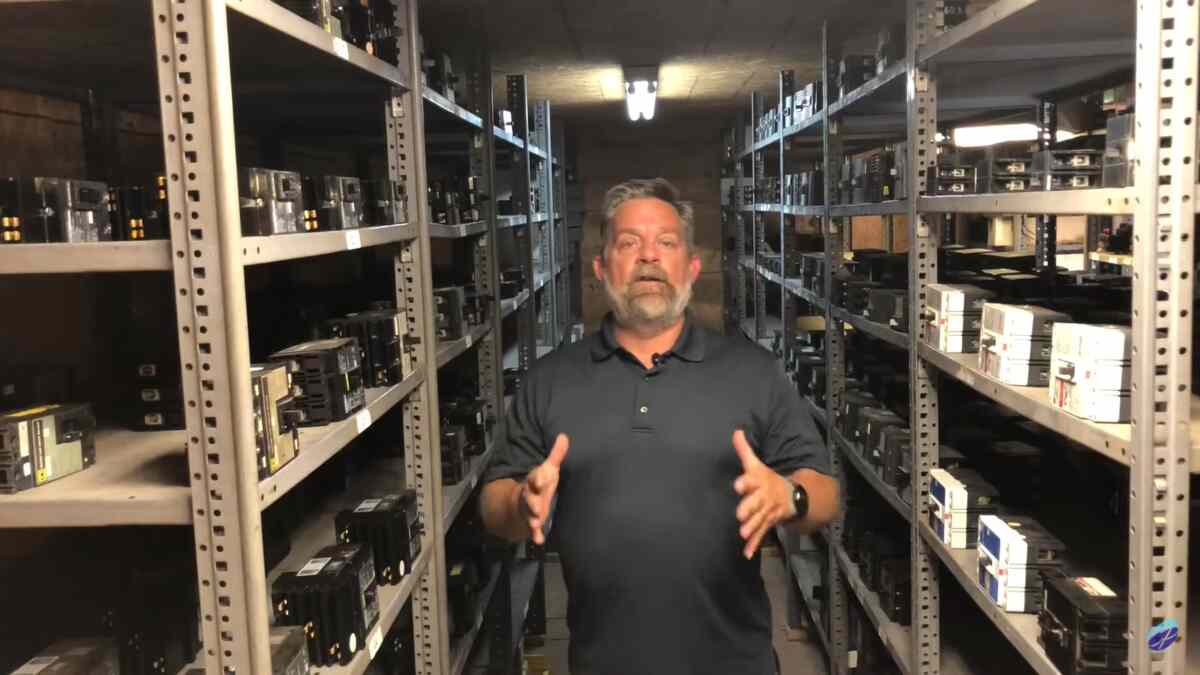
Choosing the Right Motor Starter
Selecting the right motor starter ensures safe, efficient, and reliable motor operation. The choice depends on factors such as motor size, application type, environmental conditions, and control requirements.
Motor Size and Load Type
- Small motors (≤5 HP): A Direct-On-Line (DOL) starter is ideal for simple, low-power applications.
- Medium motors (5–100 HP): A Star-Delta starter reduces inrush current and is best for industrial use.
- Large motors (>100 HP) or heavy loads: A Soft Starter gradually increases power to avoid mechanical stress.
Starting and Control Needs
- If the motor requires immediate full power, use a DOL starter.
- If a gradual start-up is needed, choose a Soft Starter or Star-Delta Starter.
- For manual control, a Manual Motor Starter is an economical option.
- If automation or PLC integration is required, opt for a contactor-based starter with overload protection.
Environmental Conditions
- Standard indoor applications: Basic enclosures are sufficient.
- Harsh environments (dust, moisture, chemicals): Use NEMA-rated or IP-rated enclosures for protection.
Energy Efficiency & Cost Considerations
- Soft Starters reduce power surges, improving energy efficiency.
- Variable Frequency Drives (VFDs) offer the best efficiency but are costlier
By considering these factors, businesses can select a motor starter that optimizes performance, extends equipment lifespan, and enhances safety.
The Role of Motor Starters in Industrial Applications
Motor starters play a critical role in industrial applications by ensuring smooth motor operation, protecting electrical systems, and enhancing energy efficiency. Electric motors power essential equipment across industries, and without proper control, sudden power surges, mechanical stress, and system failures can occur. Motor starters help mitigate these risks while optimizing performance.
Protecting Motors from Electrical Damage
When a motor starts, it can draw 6-8 times its normal operating current. This sudden inrush can overheat electrical components and shorten motor lifespan. Motor starters prevent damage by:
- Regulating voltage and current flow to avoid excessive power surges.
- Providing overload protection by cutting power if the motor draws too much current.
- Preventing phase loss issues, which can cause unbalanced motor operation.
- Example: In a manufacturing plant, a soft starter can gradually increase power to heavy-duty machinery, reducing electrical stress and improving reliability.
Improving Energy Efficiency
- Soft starters and intelligent motor controllers optimize power usage, reducing waste.
- Avoiding unnecessary high inrush currents prevents spikes in electricity costs.
- Proper motor control extends equipment life, reducing replacement and maintenance costs.
Preventing Equipment Downtime and Failures
Uncontrolled motor starts can cause overheating, short circuits, and mechanical wear. Motor starters minimize downtime by:
- Detecting motor overloads and shutting down before damage occurs.
- Providing restart protection after power failures to avoid electrical shocks.
Example: In food processing plants, motor starters ensure that conveyor belts operate without unexpected shutdowns, keeping production lines running.
Enhancing Workplace Safety
- Sudden motor failures can create hazards for machine operators.
- Motor starters have built-in safety mechanisms like emergency stops and phase failure detection.
- Controlled motor shutdowns prevent accidents.
Example: In construction sites, properly chosen motor starters prevent hazardous jolts in cranes and hoists, protecting workers and equipment.
Enabling Precision and Control
- Some processes require gradual acceleration or deceleration to avoid mechanical stress.
- Soft starters and VFDs allow precise motor speed adjustments, improving performance.
Example: In water treatment plants, motor starters help pumps start smoothly, preventing pipe damage from sudden pressure surges.
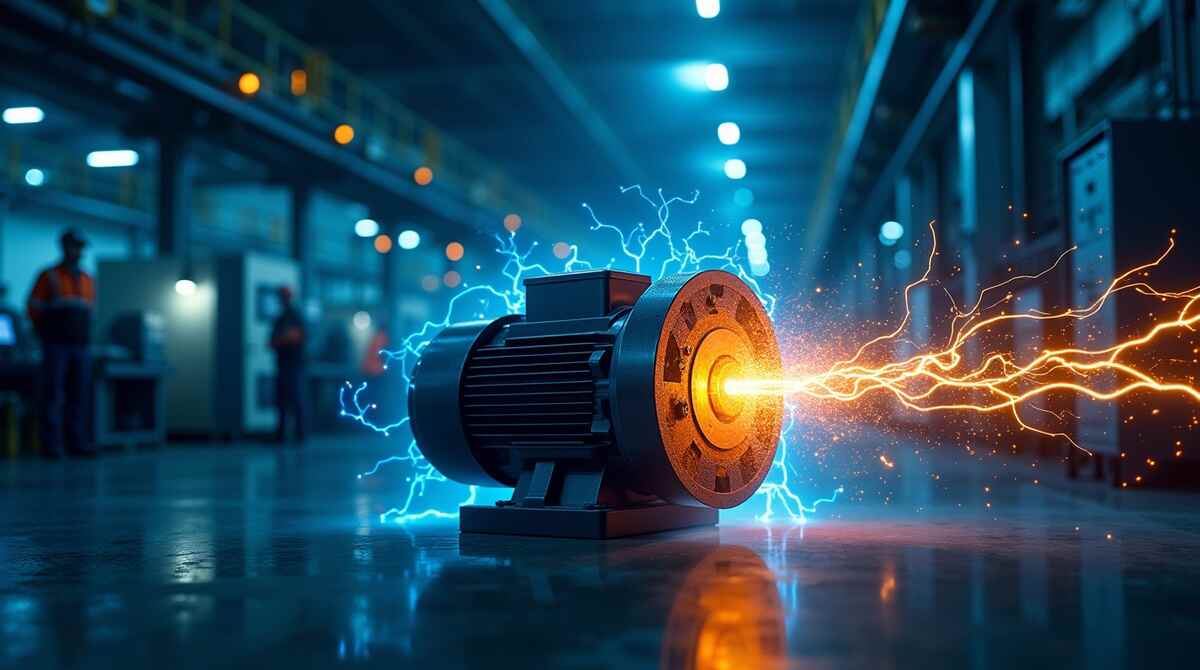
Key Functions of Motor Starters in Industrial Environments
Motor starters contribute to industrial operations in several ways:
- Protecting Motors from Electrical Surges
- When a motor starts, it can draw up to 6-8 times its normal operating current. This sudden surge can damage electrical components and reduce motor lifespan.
- Motor starters, especially soft starters, and star-delta starters, regulate voltage and current flow to prevent excessive stress on the motor.
- Benefit: Reduces wear and tear, extends motor life
- Enhancing Energy Efficiency
- Soft starters and intelligent motor controllers optimize power usage by ensuring motors only consume the energy needed for operation.
- Prevents unnecessary high inrush currents that can lead to excessive power consumption.
- Benefit: Helps industries lower electricity costs and improve energy efficiency.
- Preventing Equipment Failures and Downtime
- Motor starters with overload protection and phase failure detection automatically shut down the motor if they detect dangerous operating conditions.
- This proactive protection prevents overheating, short circuits, and motor burnout.
- Benefit: Minimizes unexpected shutdowns, improving system reliability.
- Ensuring Safe Operations for Workers
- A sudden motor failure can create hazards for machine operators and technicians.
- Motor starters include built-in safety mechanisms, such as emergency stops and controlled shutdowns, to prevent accidents.
- Benefit: Improves workplace safety and reduces the risk of electrical hazards.
- Enabling Precise Motor Control
- Some processes require gradual acceleration or deceleration to prevent mechanical stress on connected equipment.
- Soft starters help in applications where sudden motor movement could cause equipment damage.
- Benefit: Provides controlled motor operation, reducing mechanical wear.
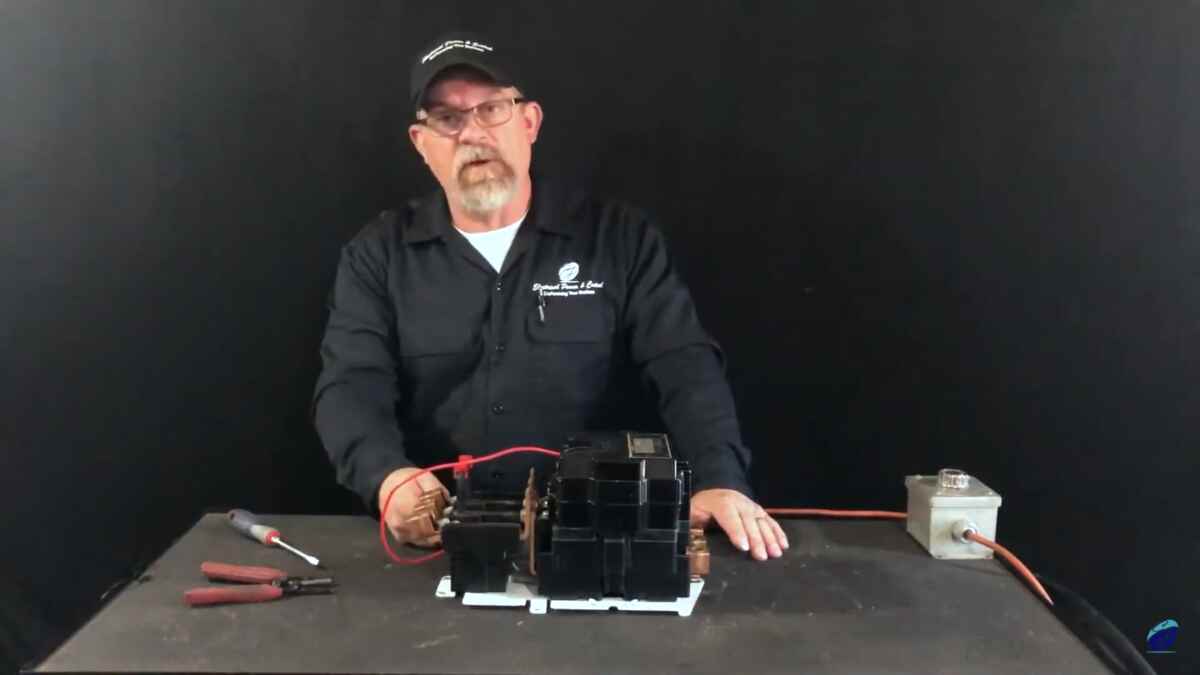
The Importance of Bench Testing Before Installation
In the world of industrial electrical systems, reliability is paramount. A minor malfunction in a motor starter can lead to downtime, operational inefficiencies, or even equipment failure. This is why bench testing is a critical step before installing a motor starter in any application. By thoroughly testing the component in a controlled environment, electrical contractors, system integrators, and facility managers can ensure the equipment performs as expected before being deployed in the field.
Why Bench Testing Matters
Bench testing serves as a proactive quality assurance measure, allowing technicians to validate the performance of a motor starter before it is installed into a larger system. This process minimizes potential failures and eliminates uncertainties, ensuring that when the motor starter is put into operation, it functions correctly and efficiently.
Key reasons why bench testing is crucial:
- Prevents Costly Downtime
- If a motor starter fails after installation, the entire system may need to be shut down for troubleshooting and replacement, causing unnecessary delays and revenue losses.
- Bench testing allows technicians to detect issues before installation, avoiding the time-consuming process of dismantling and reinstalling faulty equipment.
- Ensures Proper Functionality
- Motor starters are designed to handle significant electrical loads. Testing ensures that the contractors engage properly, overload relays function as expected, and safety features activate when necessary.
- It verifies that the starter can properly start and stop the motor, as well as regulate power flow according to load requirements.
- Reduces Installation Errors
- A technician who performs a bench test gains firsthand experience in operating the starter before installation.
- This understanding ensures that the starter is wired correctly and configured for the specific motor application, preventing improper connections that could lead to electrical hazards.
- Identifies Potential Issues Early
Some common issues that bench testing can uncover include
- Defective contactors or relays.
- Incorrect voltage ratings or wiring configurations.
- Premature tripping of overload protection.
- Faulty connections or loose terminals.
- Enhances Safety for Personnel and Equipment
- A malfunctioning motor starter can pose safety risks, including electrical shocks, fires, or damage to expensive industrial equipment.
- Testing confirms that the starter’s protective mechanisms—such as overload protection and short-circuit prevention—are functioning correctly, ensuring a safer work environment.
How to Bench Test a Motor Starter
A proper bench test follows a structured approach to evaluate the starter’s performance under simulated operating conditions. The following steps outline a systematic method for conducting a bench test:
Step 1: Gather Necessary Equipment
Before testing, ensure you have the correct tools and safety gear, including:
- A test power source (matching the voltage requirements of the motor starter).
- A test load (such as a motor simulator or an actual motor).
- Multimeter and clamp meter (for checking voltage, current, and continuity).
- Insulated gloves and safety glasses (for personal protection).
Step 2: Verify Motor Starter Specifications
- Check the voltage and current ratings of the motor starter against the system requirements.
- Confirm that the starter type (DOL, star-delta, soft starter, etc.) matches the application.
- Inspect for any visible signs of damage or component wear.
Step 3: Connect the Motor Starter to a Test Circuit
- Wire the starter as per manufacturer guidelines, ensuring that the power supply and control circuits are correctly configured.
- If applicable, connect a test motor or a simulated load to evaluate performance under real conditions.
Step 4: Perform Initial Safety Checks
- Before powering the unit, conduct a continuity test to ensure proper electrical connections.
- Check that all safety mechanisms, such as overload protection and fuses, are intact.
- Ensure that there are no loose wires or exposed terminals.
Step 5: Power On and Observe Performance
Engage the motor starter and observe the contactor operation. It should:
- Engage without excessive delay.
- Provide a smooth power transition to the motor.
- Trip the circuit in case of overload or short circuit.
- Monitor voltage and current readings to verify they align with expected values.
Step 6: Test Overload Protection
- Simulate an overload condition by gradually increasing the test load.
- The starter should trip when the load exceeds the rated current, demonstrating proper overload protection.
- Reset the starter and repeat to ensure consistent tripping behavior.
Step 7: Evaluate Phase Loss Protection (If Applicable)
- If testing a three-phase motor starter, disconnect one phase and observe whether the starter detects the loss and shuts down.
- This step ensures that the starter prevents damage from phase imbalance.
Step 8: Record and Verify Results
- Document voltage, current, and tripping thresholds for reference.
- Confirm that the starter operates within manufacturer specifications.
- If any abnormalities arise, additional troubleshooting is performed before field installation.
Conclusion
After understanding the importance of motor starters in industrial applications, it’s valuable to delve deeper into the practical aspects of their usage. One of the key steps before installing a motor starter is bench testing.
Our video tutorial, “Bench Testing a NEMA Size 4 Motor Starter,” provides an in-depth guide on this process, offering practical insights and step-by-step instructions. We encourage you to watch this video and deepen your understanding of motor starters and the bench testing process. Your journey towards mastering motor starters continues there.