Table of Contents
ToggleIndustrial automation has revolutionized the manufacturing sector by streamlining processes and enhancing overall efficiency. Defined as the use of various control systems for operating equipment such as machinery and processes in factories, automation plays a crucial role in boosting productivity, quality, safety, and overall output in industrial settings.
What is Industrial Automation?
Industrial automation refers to the technology by which a process or procedure is performed without human assistance. It involves using computer software and machinery to guide and control various industrial processes.
At the core of industrial automation is the desire to improve efficiency and reliability in manufacturing. It leverages technologies such as robotics, control systems, and information technologies to handle tasks that were once manual, repetitive, or dangerous.
This transition enables many industries to achieve mass production with minimal human intervention. Automation manufacturing is particularly significant because it allows for consistent quality and precision.
Mechanics of Automation
The mechanics of automation lie in the systems and processes that allow machines to perform tasks autonomously. This typically involves three key components: sensors, control systems, and actuators.
Components
- Sensors: These act like eyes and ears for the machines, gathering data from the environment or the machines themselves. This data can include things like temperature, pressure, position, or presence/absence of objects.
- Control Systems (PLCs): Programmable logic controllers are the brains of the operation. They receive data from the sensors, run it through programmed algorithms, and send instructions to the actuators.
- Actuators: These are the muscles that perform the physical actions. They can be motors, valves, grippers, or any other mechanism that can move or control something based on the control system’s instructions.
Feedback Loops
- Automation systems often incorporate feedback loops to continuously monitor and adjust themselves.
- Sensors provide data on the outcome of the action taken by the actuators.
- This data is fed back to the control system, allowing it to verify successful completion or make adjustments if there are deviations.
- Feedback loops play a vital role in ensuring accuracy and maintaining consistent operation.
As industries increasingly adopt automation manufacturing, they integrate these mechanics into existing workflows, transforming how factories and plants operate by increasing speed, precision, and efficiency.
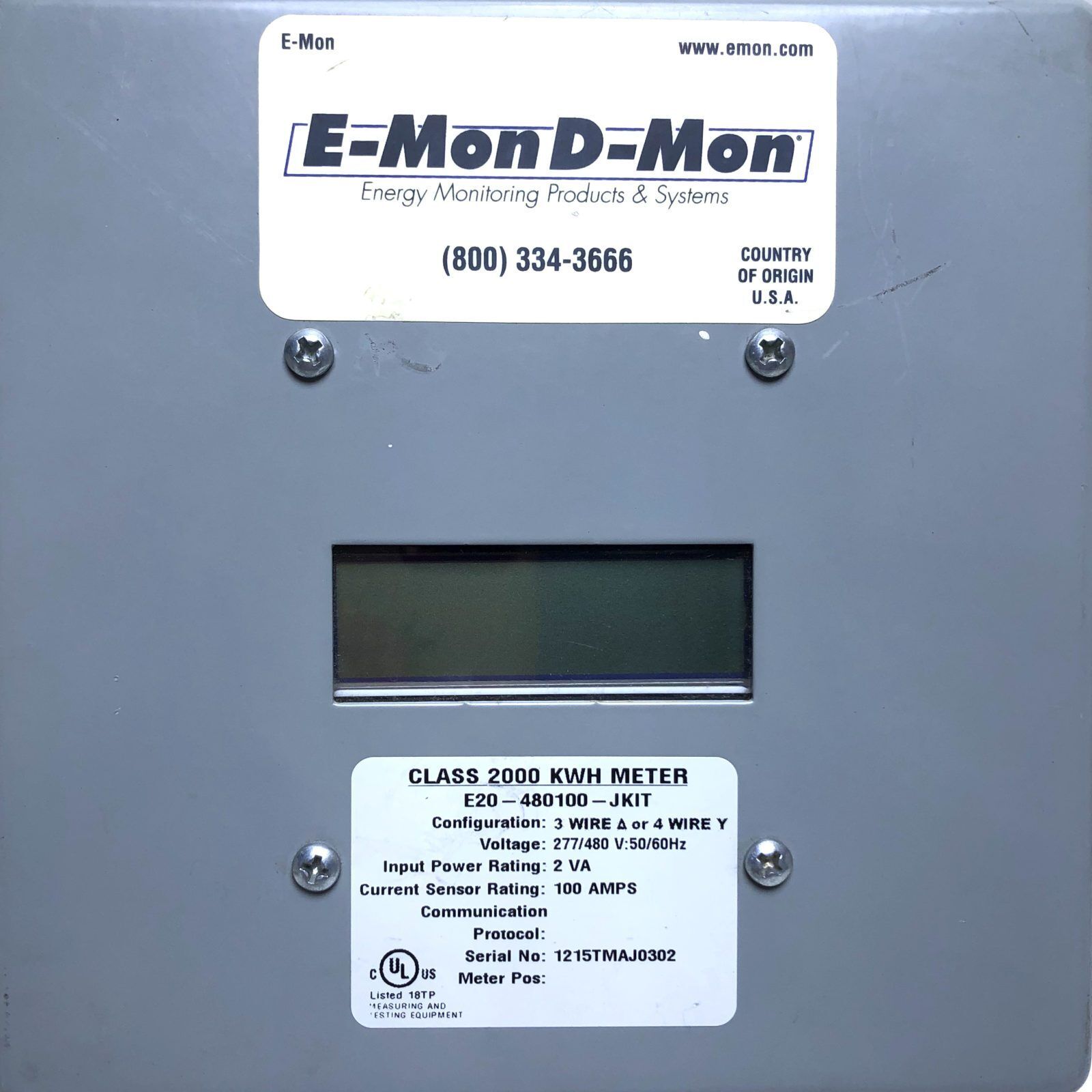
Automation for Efficient Manufacturing
Automation has a profound impact on manufacturing efficiency by enabling faster production times, reducing the likelihood of errors, and allowing for 24/7 operation without the constraints of human labor.
Automated systems are designed to perform repetitive tasks with precision and without fatigue, leading to a substantial increase in production rates. Automation manufacturing allows for better use of materials and resources, as precise control minimizes waste and optimizes the use of raw materials.
In addition, automated equipment can be quickly reprogrammed to adapt to new production requirements, making it possible for factories to switch between products and processes with minimal downtime. This flexibility enhances a company’s ability to respond to market changes and customer demands.
Overall, the impact of automation on efficiency is not just about doing things faster; it’s about doing them smarter and with greater agility.
Quality Control Through Automated Systems
Automated systems significantly enhance quality control in manufacturing by providing consistent production parameters and minimizing human error. These systems can continuously monitor and adjust processes to ensure that the product meets strict quality standards.
Also, data collected by automated systems can be used for real-time process optimization, as well as for long-term quality improvement initiatives. By analyzing this data, manufacturers can identify patterns and root causes of defects, leading to better product designs and manufacturing processes.
Automation ensures that every item produced adheres to the same high standard, resulting in increased customer satisfaction and a stronger reputation for quality in the marketplace.
How Automation Enhances Industrial Safety
Automation plays a vital role in enhancing safety in industrial settings. By taking over dangerous tasks, such as handling heavy machinery or toxic substances, automated systems can reduce the risk of workplace injuries. These systems can operate in hazardous environments where conditions might be unsafe for humans, such as extreme temperatures, high altitudes, or areas with potential chemical exposure.
As well, automation provides consistency in operations, which is crucial for maintaining safety standards. With fewer variables introduced by human labor, processes are less prone to the unpredictability that can lead to accidents. Automated systems are also equipped with safety sensors and emergency stop features that can halt operations if a potential hazard is detected.
By reducing the need for human presence in risky areas and ensuring consistent adherence to safety protocols, automation directly contributes to creating a safer work environment.
The Productivity Pyramid: How Automation Fuels Growth
Automation acts as a catalyst for productivity, creating a pyramid effect where benefits at the foundation level lead to greater advantages at each subsequent level.
At its base, automation reduces the time taken to complete tasks and increases the volume of production. This increase in throughput is critical in meeting rising demand without compromising on quality or delivery times.
Moving up the pyramid, the data collected from automated processes enables better decision-making and process optimization. This intelligence fuels continuous improvement cycles and propels productivity gains.
At the pinnacle, the strategic integration of automation fosters innovation, allowing companies to explore new products and services that wouldn’t have been feasible with manual operations.
This pyramid of productivity not only signifies increased output but also represents the value added at each stage of production, from operational efficiency to market competitiveness and innovation.
Automation, therefore, is not just an operational change; it’s a strategic transformation.
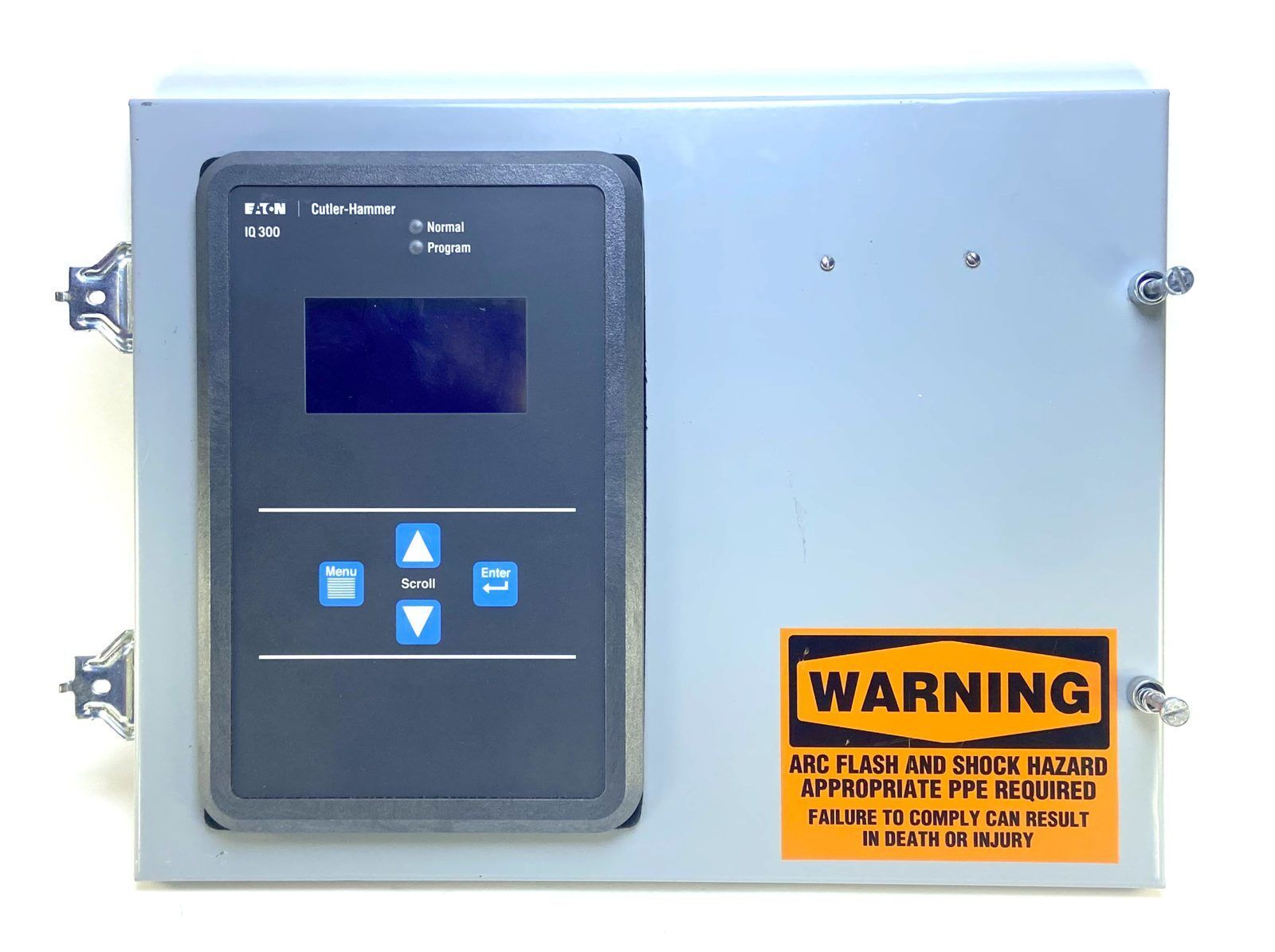
How Automation Cuts Expenses
Automation directly contributes to cost savings in several ways. Initially, it might seem like a significant investment, but the long-term savings are substantial. Automated systems work at a constant pace without breaks, sick days, or vacation time, which means they can produce more over the same period than a human workforce. This increase in productivity lowers the cost per unit of production.
In addition, automation minimizes waste by improving precision in the use of materials and reducing errors that lead to product defects. Maintenance costs also go down, as automated systems can be more reliable and less prone to breakdown than manual operations. Over time, the reduction in operational costs due to fewer errors, less waste, and increased production efficiency can lead to significant financial savings for a business.
Automation is an investment in future savings and increased profitability.
The Automation Revolution
The role of automation in industrial efficiency cannot be overstated. It has become a cornerstone of modern manufacturing, offering unparalleled consistency, precision, and speed. Automation reduces the reliance on manual labor, mitigates human error, and paves the way for continuous operation, leading to increased productivity and profitability.
Want to learn other ways to increase productivity? Read our article on electrical enclosures, where you can find out how to increase productivity while reducing downtime, preventing damage, and promoting the safety of both equipment and personnel.