Table of Contents
ToggleImagine you’re deep into a facility upgrade. The project is running behind, your client’s breathing down your neck, and a circuit breaker just failed. You’re short on replacements. But sitting on a shelf in your maintenance room? A nearly identical breaker that was swapped out months ago—still in solid shape.
In moments like these, the question comes up fast: Can we safely reuse this component?
With industrial budgets tightening, supply chains tightening even more, and sustainability initiatives gaining momentum, the idea of reusing electrical components isn’t just smart—it’s increasingly necessary. But not all components are created equal. Some can be reused safely with a proper inspection. Others? Not worth the risk.
This guide is here to help you understand which industrial electrical components can (usually) be reused safely, how to evaluate them, and when to replace them instead. Whether you’re managing a facility or coordinating multiple job sites, knowing where reuse is safe can save you serious time and money, without compromising reliability.
Let’s dig in.
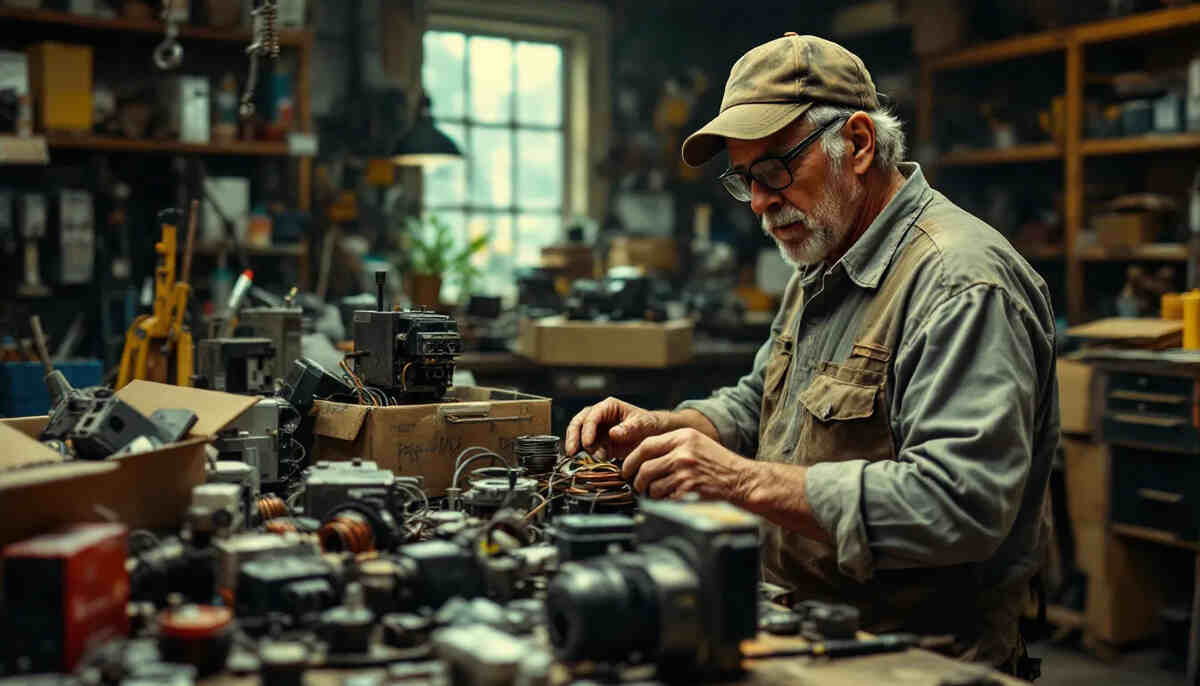
Why Reuse Industrial Electrical Components?
In today’s industrial environment, every second of downtime costs more than money—it risks contracts, damages reputations, and puts intense pressure on already tight project schedules. When margins are thin and supply chains are unpredictable, knowing which components you can reuse becomes a competitive advantage.
The Benefits of Reuse
- Cost Efficiency: Replacing components adds up fast. Reuse, when safe, can stretch your budget further—especially on large-scale retrofits or maintenance overhauls.
- Shorter Downtime: When a part fails mid-project, having a reusable component on hand can shave hours (or days) off your schedule.
- Sustainability Goals: More companies are focusing on ESG strategies. Reusing electrical parts reduces e-waste and supports a circular economy.
- Supply Chain Workarounds: Long lead times and backorders can bring projects to a halt. Reuse gives you a backup plan—one you already own.
The Risks of Cutting Corners
But here’s the catch—reuse without proper evaluation can cause serious issues.
- Safety Hazards: A degraded breaker or connector could fail under load, creating arc flash risk or equipment damage.
- Compliance Concerns: Reusing parts without documentation or reconditioning might violate OSHA, NEC, or insurance policies.
- Unpredictable Performance: Not all wear is visible. Components that look fine may have unseen issues from prior heat cycles, vibration, or overloads.
Reusing industrial components isn’t about cutting corners—it’s about knowing the difference between safe reuse and unsafe risk. With the right checks, you can keep your operations moving without compromising safety or performance.
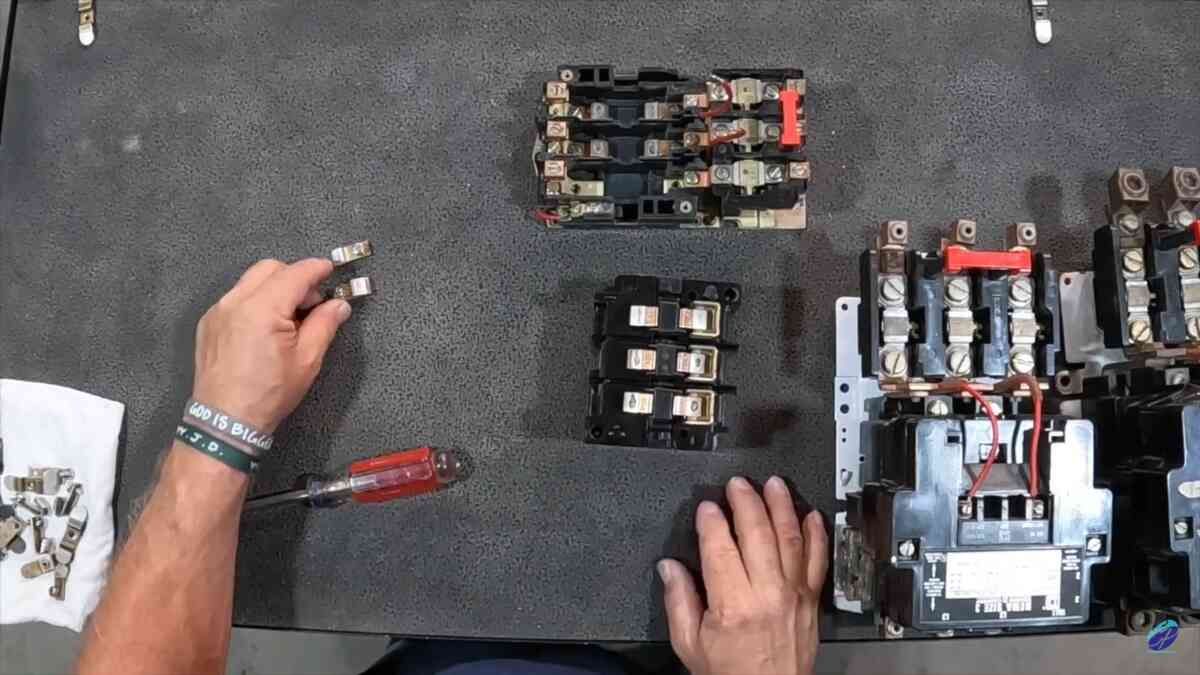
How to Evaluate Component Reusability
Not all electrical components are created equal, and not all wear and tear is visible. Before you reuse a part in a critical system, it’s essential to inspect, test, and verify its condition. Here’s how to determine what stays on the shelf and what goes in the scrap bin.
Step 1: Perform a Visual Inspection
Start with a detailed external check. Look for:
- Signs of overheating: discoloration, melting, or scorch marks
- Cracks or corrosion on plastic housings, metal terminals, or fasteners
- Worn contact points or terminals
- Missing labels or part numbers that could affect traceability
- Contaminants like dust, oil, or moisture, especially in enclosures
Quick Tip: Use a magnifying lens or inspection camera to examine internal mechanisms, especially on components like breakers or contactors.
Step 2: Functional Testing
If the component passes visual inspection, verify that it performs as expected:
- Use a multimeter or insulation resistance tester to check continuity, resistance, or shorts.
- Cycle moving parts (e.g., switches, contactors) to ensure smooth, reliable operation.
- For more complex parts like motor starters or relays, test under load conditions if possible, simulating real-world operation.
Example: A contractor reused contactors that looked pristine—but load testing revealed delayed coil response, indicating internal coil fatigue.
Step 3: Check Documentation and Certifications
Reused parts should still comply with safety and regulatory standards:
- Look for manufacturer guidelines on reuse or lifespan.
- Check the latest NEC and UL guidelines on acceptable reuse or reconditioning.
- Ensure the component has identifiable serial numbers or lot numbers for traceability.
If a part was previously reconditioned, confirm that it came from a certified provider—and request a service report.
Step 4: Use Diagnostic Tools (When Available)
Some components benefit from deeper diagnostics, especially in industrial settings:
- Thermal imaging can detect internal heat buildup
- Vibration testing helps assess internal wear in mechanical assemblies
- Dielectric testing may reveal insulation degradation
These tools are especially useful in preventive maintenance workflows and for facilities aiming for proactive asset management.
Red Flags That Disqualify Reuse
Even if a part seems fine, here are signs it should not be reused:
- It was removed due to failure or unknown issues
- It shows signs of arcing or exposure to fault currents
- It no longer meets current ratings or standards
- You can’t confirm its origin, certification, or history
Build Reusability Into Your Workflow
Instead of making reuse decisions on the fly, consider implementing a formal component inspection protocol within your inventory management process. This might include:
- Predefined inspection checklists by component type
- Labeling or tagging tested components
- Creating a “Ready for Reuse” shelf section
- Partnering with third-party testing labs for critical parts
Pro Tip: Empower your technicians with a mobile checklist to streamline inspections in the field or at the warehouse.
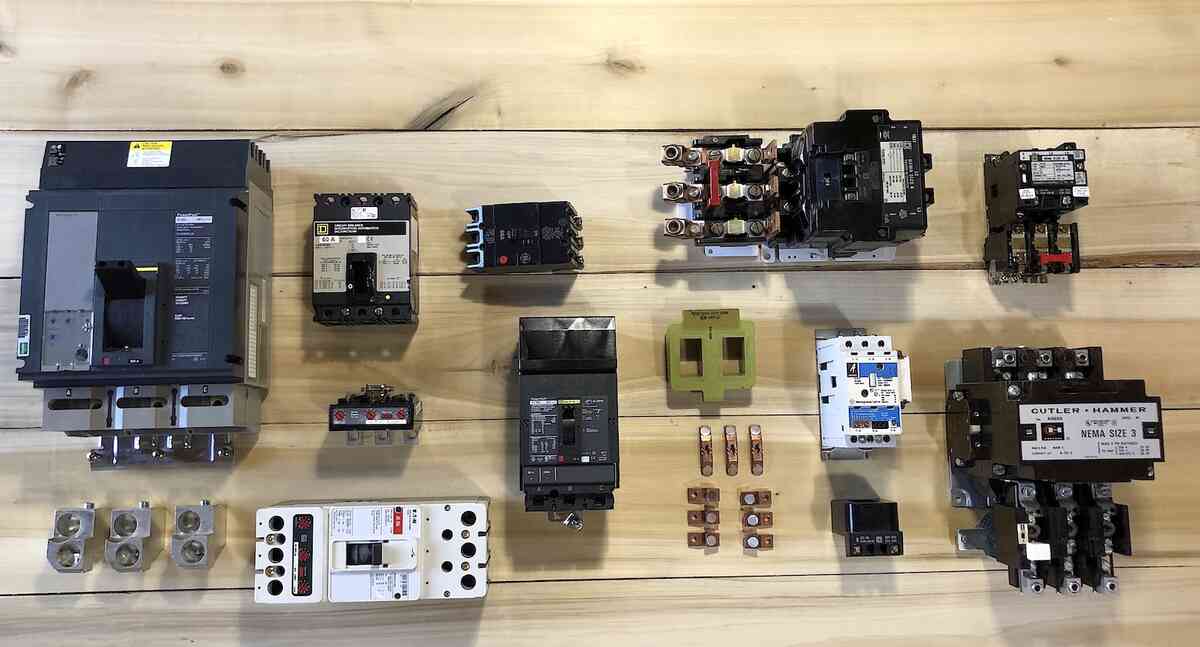
7 Commonly Reused Components (and Why)
These seven components are among the most commonly reused in industrial environments. With the right inspection and maintenance, they can safely offer a second (or third) life, saving you time, money, and unnecessary waste.
Circuit Breakers
What It Does:
Circuit breakers are the frontline defense in any electrical system. They interrupt current flow during overloads or short circuits to protect equipment, wiring, and personnel.
Why It’s Often Reused:
Industrial-grade breakers (especially molded-case or insulated-case models) are engineered to handle thousands of mechanical operations. They’re often pulled during system upgrades, not because they failed, just because specs changed.
Before Reuse:
- Trip Testing: Use a primary injection tester or secondary current injection test to verify accurate trip curves.
- Visual Inspection: Look for carbon scoring, arc flash marks, or wear on toggle mechanisms.
- Label Verification: Confirm legibility of UL/CSA labels for amp rating, interrupting capacity, and date codes.
- Manufacturer Reference: Check OEM guidelines for reusability or refurbish cycles.
When Not to Reuse:
- If it has experienced a high-fault interruption
- If there’s deformation near terminals (a sign of heat damage)
- If the trip mechanism fails under test
- If stored in uncontrolled environments for long periods (moisture exposure can damage internals)
Pro Tip: For reused breakers, always log test results and label units with inspection dates.
Contactors and Relays
What They Do:
Contactors switch large loads (e.g., motors, HVAC, lighting), while relays handle low-power signals in control circuits.
Why They’re Reused:
Their modular design allows individual components (coils, contacts, arc chutes) to be replaced or maintained. Quality contactors can outlast a machine if not exposed to harsh cycles.
Before Reuse:
- Mechanical Actuation: Manually energize and de-energize the coil; listen for clean, crisp clicking sounds.
- Contact Wear: Open the housing (if permitted) to inspect contact points for pitting or welding.
- Coil Resistance Check: Use an ohmmeter to ensure coil resistance is within OEM spec.
- Mounting Surface: Confirm the base is flat and secure to avoid misalignment.
When Not to Reuse:
- Coils buzz or show discoloration (sign of internal heat damage)
- Contacts are fused or excessively worn
- No part numbers are visible for reordering or traceability
Scenario: A system integrator reused a relay during a temporary panel install, but intermittent contacts caused nuisance trips. Replacing it with a tested unit solved the issue.
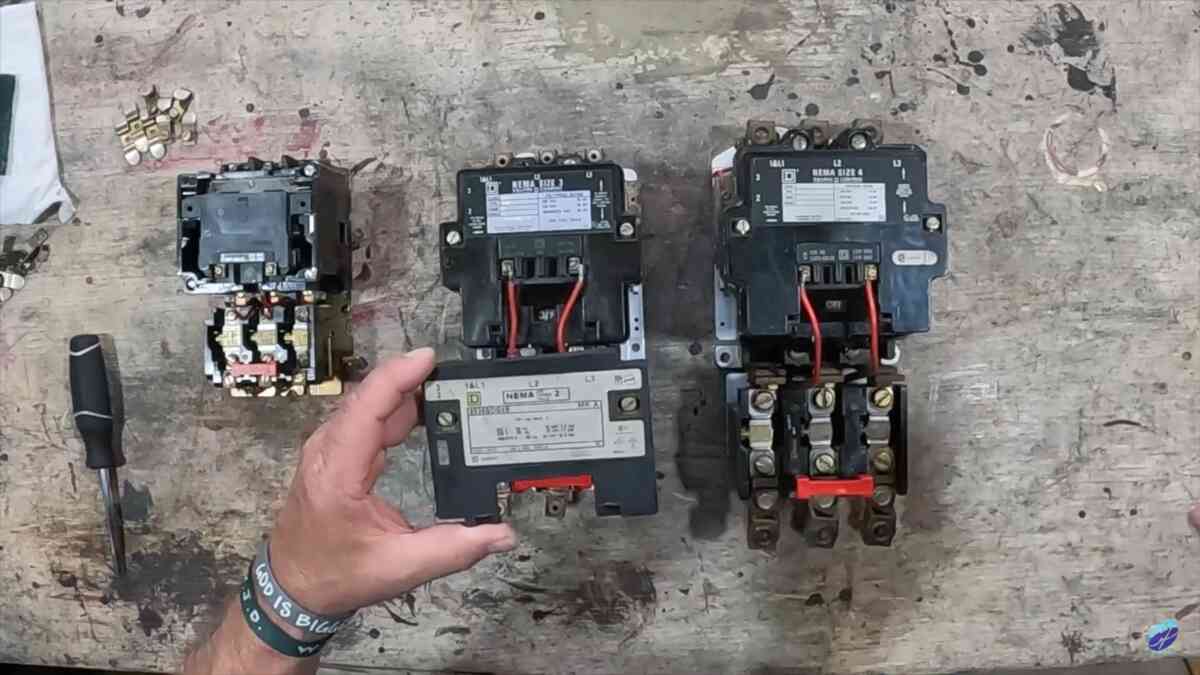
Motor Starters
What They Do:
Motor starters combine contactors with overload protection to manage motor starts and stops, especially for 3-phase applications.
Why They’re Reused:
They’re built for longevity, often removed only when motors are decommissioned or control schemes change.
Before Reuse:
- Thermal Overload Unit: Inspect and reset test to ensure trip calibration is intact.
- Contact Surfaces: Look for discoloration, surface pitting, or welding.
- Auxiliary Contacts: Confirm accessory points (like NC/NO blocks) still function reliably.
- Control Terminals: Ensure tight, corrosion-free screw connections.
When Not to Reuse:
- If thermal units are cracked, warped, or missing
- If contacts show blueing (indicates overheating or arc)
- If the starter size doesn’t match the motor being controlled
Pro Tip: Label reused starters with motor specs and previous load data when available. This helps ensure compatibility on redeployment.
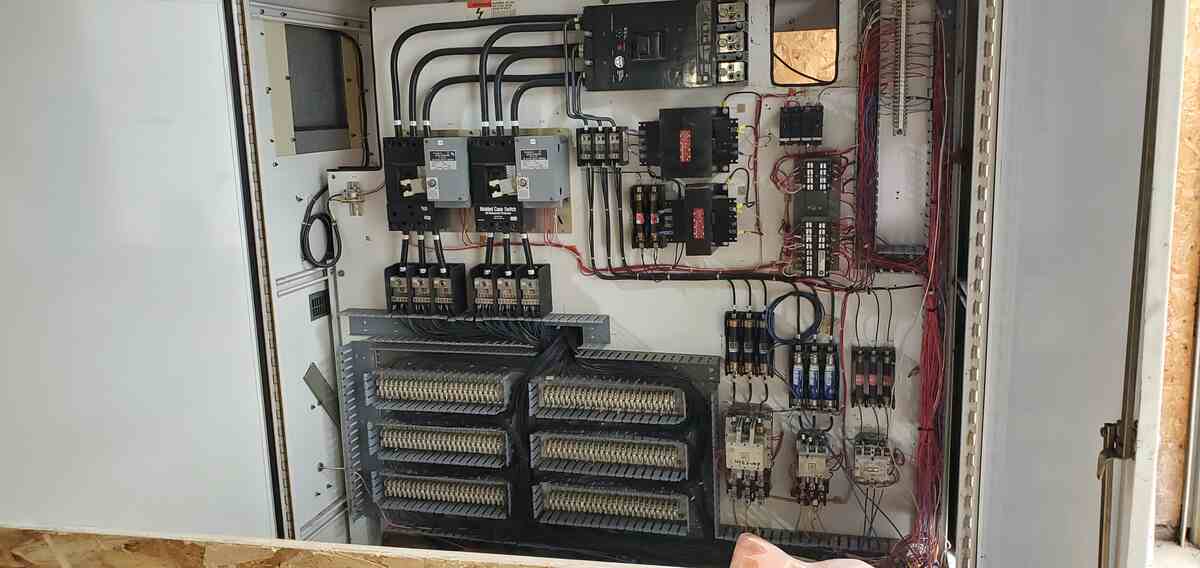
Industrial Enclosures
What They Do:
Enclosures (NEMA/IP rated) protect internal components from dust, water, and mechanical damage. Common in MCCs, control panels, and field junction boxes.
Why They’re Reused:
They’re usually rugged, made from powder-coated steel or fiberglass, and expensive to replace. Reuse is a no-brainer when they’re structurally sound.
Before Reuse:
- Seal Check: Test door gaskets for elasticity and compression.
- Surface Condition: Sand down and repaint minor rust to prevent spread.
- Door Hardware: Verify hinges, clamps, and locks operate smoothly.
- Knockout Integrity: Plug any unused holes to maintain ingress protection.
When Not to Reuse:
- Significant rust-through or corrosion around seams
- Degraded gaskets (flattened, cracked, missing)
- Warped door frames that don’t seal evenly
Scenario: An industrial facility reused Type 12 enclosures during an upgrade, after replacing gaskets and repainting panels, cutting panel costs by 40%.
Terminal Blocks
What They Do:
These blocks terminate wiring in control cabinets and power panels. They’re essential for maintaining organized, serviceable connections.
Why They’re Reused:
They are static components—no moving parts, and made from high-durability polymers and brass/copper alloy connectors.
Before Reuse:
- Tightness Test: Use a torque driver to ensure terminal screws still hold tension.
- Marking Legibility: Check for readable wire numbers or color codes.
- Continuity Test: Confirm internal bus bars conduct properly.
When Not to Reuse:
- Plastic cracking or chipping
- Terminal screws spin or strip
- High-resistance connections were found on inspection
Pro Tip: Replace terminal jumpers or end stops as needed—they’re cheap insurance for system reliability.
Wiring and Conduits
What They Do:
They conduct electrical energy and protect conductors in industrial settings, running between motors, panels, controls, and sensors.
Why They’re Reused:
Conduit (especially EMT or rigid) and stranded copper wire are highly durable when properly installed and protected. They can outlive the equipment they connect.
Before Reuse:
- Visual Inspection: Look for insulation nicks, UV degradation, or discoloration.
- Insulation Resistance Test: Use a megohmmeter to verify cable health, especially for motor or feeder wiring.
- Conduit Integrity: Ensure threads are clean, no rust inside, and no crushing along runs.
When Not to Reuse:
- Cable jackets are brittle or deformed
- Markings are illegible (affects code compliance)
- The cable length was cut too short for safe termination
Scenario: A contractor recovered 500 feet of THHN cable after a line teardown. After IR testing and re-labeling, they safely reused it on a subpanel—saving both material and delivery time.
Pushbuttons and Selector Switches
What They Do:
These interface components are used by operators to control machinery and systems, from E-stops to mode selection.
Why They’re Reused:
They’re mechanically simple, often panel-mounted in protected environments, and easy to test for functionality.
Before Reuse:
- Actuation Check: Press and release several times to test spring-back and engagement.
- Contact Blocks: Inspect for corrosion or pitting.
- Mounting Threads: Confirm a tight fit and no cracks in the plastic or metal bezels.
When Not to Reuse:
- Mushy or sticky operation
- Contacts no longer “snap” open/closed
- Labels worn or illegible, especially for critical functions like E-stops
Pro Tip: Clean pushbuttons using electronics-safe contact cleaner—just don’t soak them, especially if unsealed.
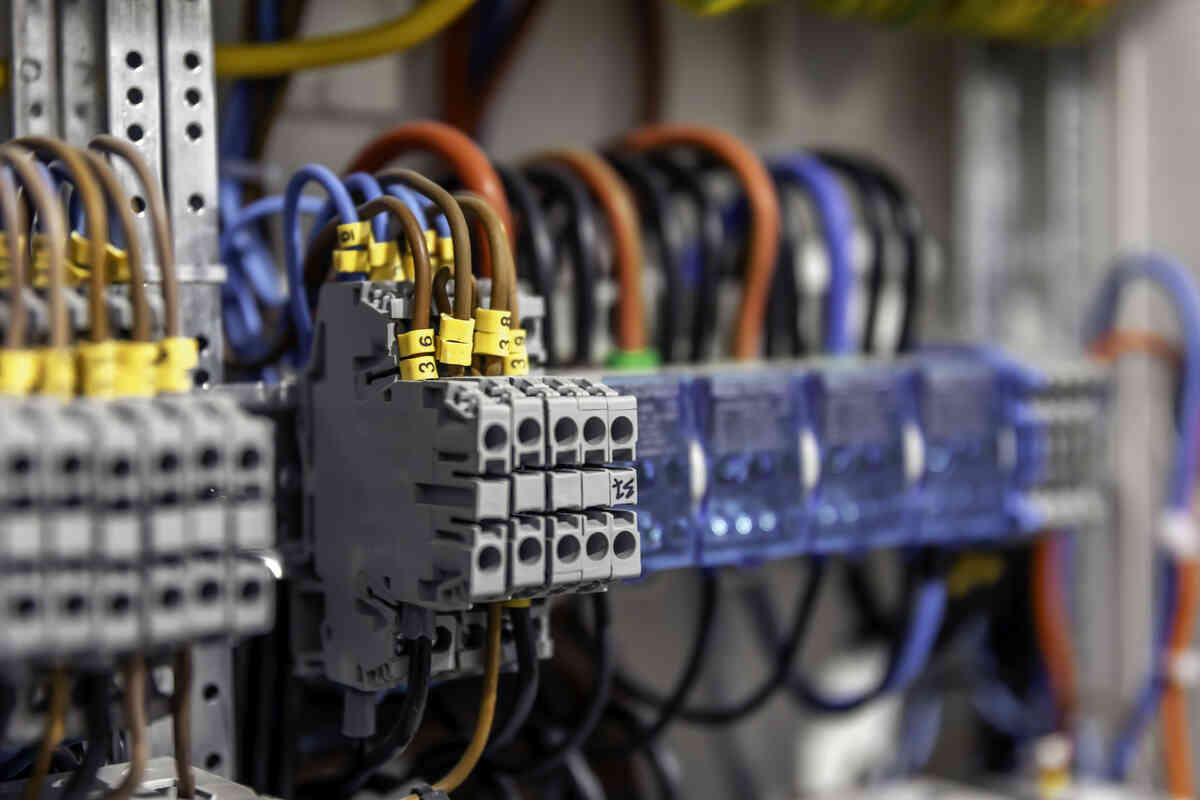
What Not to Reuse
While many electrical components are built for durability, others are specifically designed to be replaced, not reused. Reusing them, even with good intentions, can introduce hidden risks that lead to equipment failure, regulatory violations, or worse—safety hazards.
Here are the components that should never be reused under normal circumstances:
Fuses
Why Not:
Fuses are one-time-use protective devices. Even if a fuse hasn’t visibly blown, it may have experienced thermal stress that affects its future response.
Risks of Reuse:
- Unpredictable performance under fault conditions
- Increased risk of delayed or no interruption during overcurrent
- Potential voiding of UL/NRTL compliance
Pro Tip: Always keep a stock of manufacturer-specified replacements for each fuse type. Never “guess” if a fuse is still good.
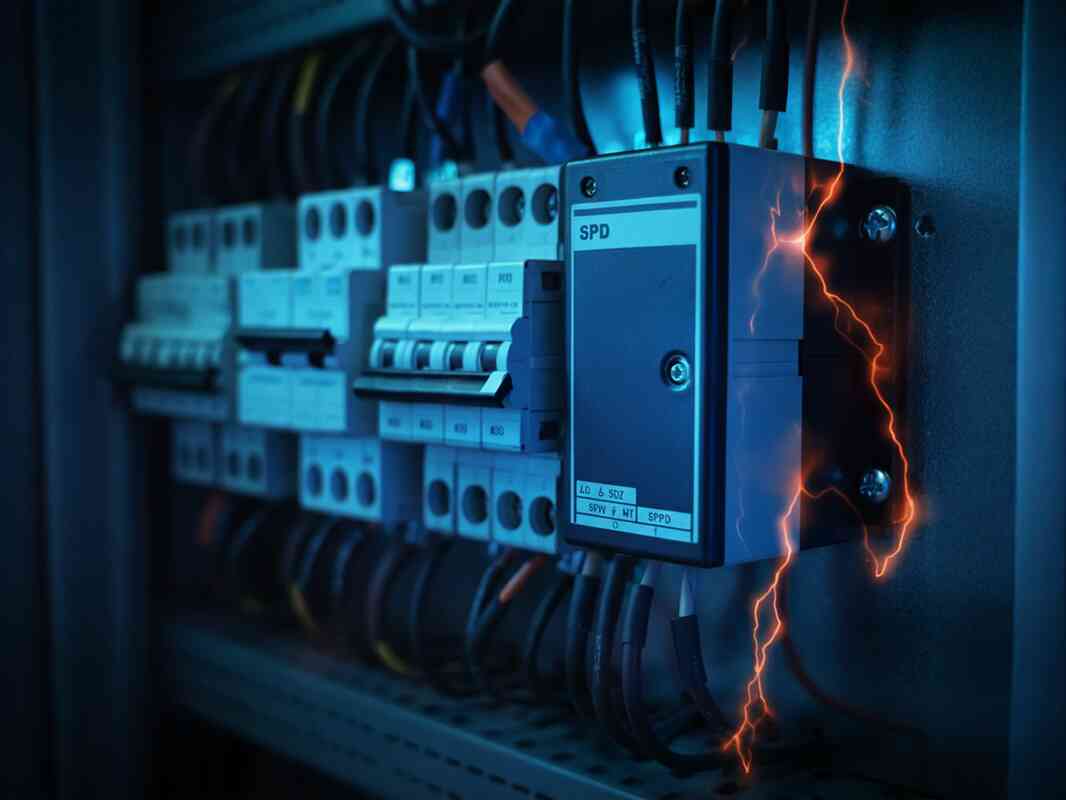
Surge Protection Devices (SPDs)
Why Not:
Surge protectors degrade each time they absorb a transient voltage spike. The internal MOVs (Metal Oxide Varistors) deteriorate silently, meaning they may appear fine but be completely ineffective.
Risks of Reuse:
- No protection during the next surge event
- May compromise upstream equipment (VFDs, PLCs, HMIs)
- Some insurance carriers prohibit reuse altogether
Watch For: Indicators like LED status lights or alarms—if anything’s off, replace the SPD immediately.
Electrolytic Capacitors
Why Not:
These are particularly sensitive to heat, voltage irregularities, and aging. Even when they’re pulled from lightly used boards, electrolytic capacitors degrade internally over time.
Risks of Reuse:
- Voltage leaks or short circuits
- Increased ripple current or poor power factor correction
- Damage to circuit boards or power supplies
Pro Tip: If you’re rebuilding a power supply or drive panel, always replace aged capacitors, especially if they’re more than 3–5 years old.
Any Component Exposed to Arc Flash or High-Fault Current
Why Not:
Arc flashes or fault currents can cause invisible internal degradation. Housing may look fine, but terminals could be welded, insulation could be compromised, or internal mechanicals may be unstable.
Risks of Reuse:
- Secondary failure during reinstallation
- Electrical fires, shock hazards, or unexpected shutdowns
- Violation of safety standards and liability issues
Scenario: A facility unknowingly reused an enclosure from a faulted panel—the internal DIN rail collapsed under the vibration of new equipment, leading to a line-wide short circuit.
Components with Unknown History or Origin
Why Not:
Without documentation, you can’t confirm if a component was exposed to overvoltage, incorrect installation, or poor environmental conditions.
Risks of Reuse:
- Regulatory non-compliance during audits or inspections
- Functional inconsistencies during operations
- Possible insurance disqualification after incidents
Rule of Thumb: If it doesn’t have a part number, test history, or recognizable markings, don’t reinstall it.
The Bottom Line
Some parts are meant to be reused with care, while others are engineered to sacrifice themselves for system protection. Knowing the difference helps you:
- Avoid expensive mistakes
- Protect your team and assets
- Build a reputation for doing things right—not cutting corners
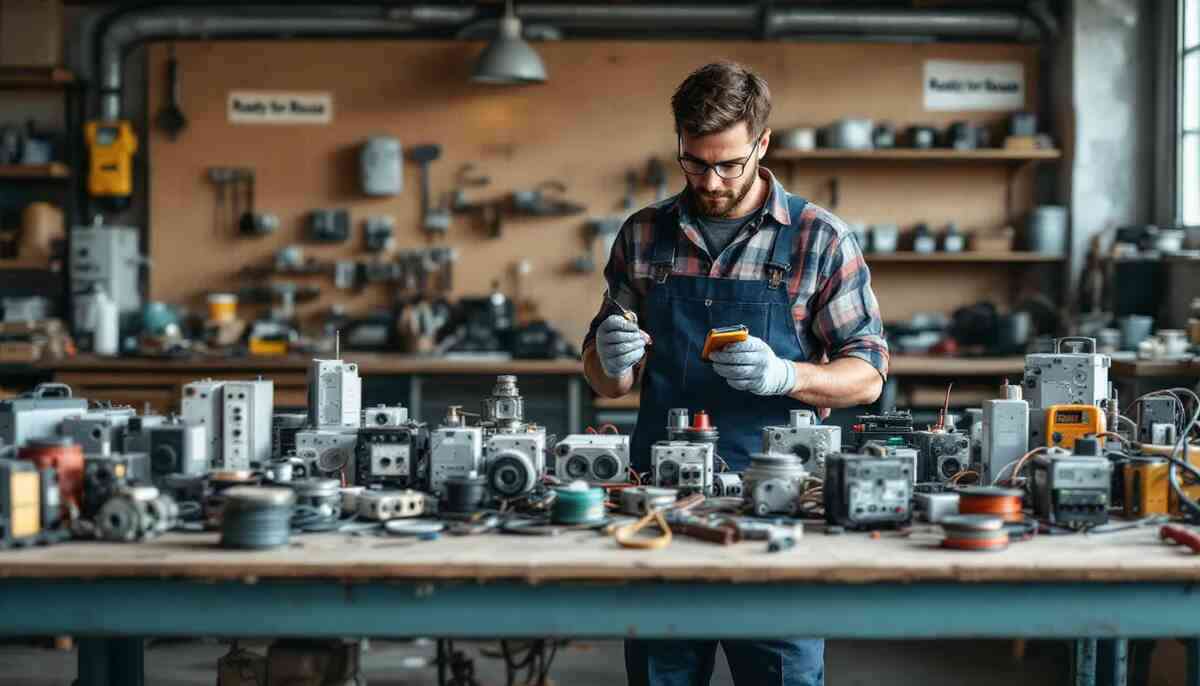
Tips for Safe Reuse
Reusing electrical components can be a smart strategy—but only if it’s done methodically and backed by a process. Whether you’re managing a maintenance team or a field crew across multiple job sites, these practices will help ensure every reused component is safe, reliable, and compliant.
Document Everything
Why it matters:
Traceability reduces liability and improves system transparency, especially for critical components.
Best practices:
- Label reused components with inspection/test dates and initials
- Keep photos of reused items pre- and post-inspection
- Use barcodes or QR codes to track reconditioned items in your CMMS
Pro Tip: Create a digital “Reuse Log” that your team can update from the field—simple spreadsheets or CMMS integrations work great.
Implement a Standard Reuse Protocol
Why it matters:
Consistency ensures nothing gets overlooked—and helps new team members follow the same quality checks.
What to include in your SOP:
- Visual inspection checklist
- Functional and electrical test steps
- Documentation and re-labeling steps
- Reuse eligibility criteria by component type
Example: One facility cut its panel downtime by 25% by tagging pre-approved reused components with color-coded labels: Green = Good to Go, Yellow = Needs Testing, Red = Scrap.
Use Certified Reconditioning Partners When Needed
Why it matters:
Some components—especially breakers, relays, or starters—can be professionally reconditioned to like-new condition for a fraction of replacement cost.
What to look for:
- UL 508 or 1066 compliance (depending on component type)
- Full service reports and certifications
- Warranty or guarantee of performance
Scenario: A system integrator reused $12,000 worth of MCC buckets that had been reconditioned to OEM specs—saving costs and meeting NEC reconditioning guidelines.
Educate Your Team on Reuse vs. Replace Decisions
Why it matters:
Technicians often make split-second calls—empowering them with clear guidance avoids inconsistent reuse decisions.
Action steps:
- Conduct reuse training during toolbox talks or shift meetings
- Share visual examples of what “good” and “bad” reuse looks like
- Reinforce that safety and performance come before cost savings
Pro Tip: Include reuse criteria in technician training programs, alongside lockout/tagout and PPE protocols.
Align with Compliance and Insurance Guidelines
Why it matters:
Regulatory bodies like NEC, OSHA, and UL have strict rules about what’s allowed—and your insurance carrier might, too.
Best practices:
- Review reusability guidelines annually based on the latest NEC code cycle
- Avoid reusing any component tied to life safety or overcurrent protection
- Consult with your insurance provider on reuse policies for critical systems
Cautionary Tale: An insurance claim was denied when a reused SPD failed and caused a $60K equipment loss, because there was no documentation on its condition or testing.
Build Reuse into Your Maintenance and PM Workflow
Why it matters:
Reuse should be proactive, not just a crisis response.
What to do:
- Add reuse evaluations to preventive maintenance (PM) schedules
- Create a “Reuse-Ready Inventory” zone with tagged and tested components
- Rotate tested spares to avoid long-term shelf degradation
Bonus: This adds value to your sustainability efforts—documenting reuse supports ESG reporting and waste reduction targets.
With the right tools, training, and tracking, reusing components becomes a strategic advantage, not a shortcut. It empowers your team to move faster, spend smarter, and operate with confidence—without sacrificing reliability or compliance.
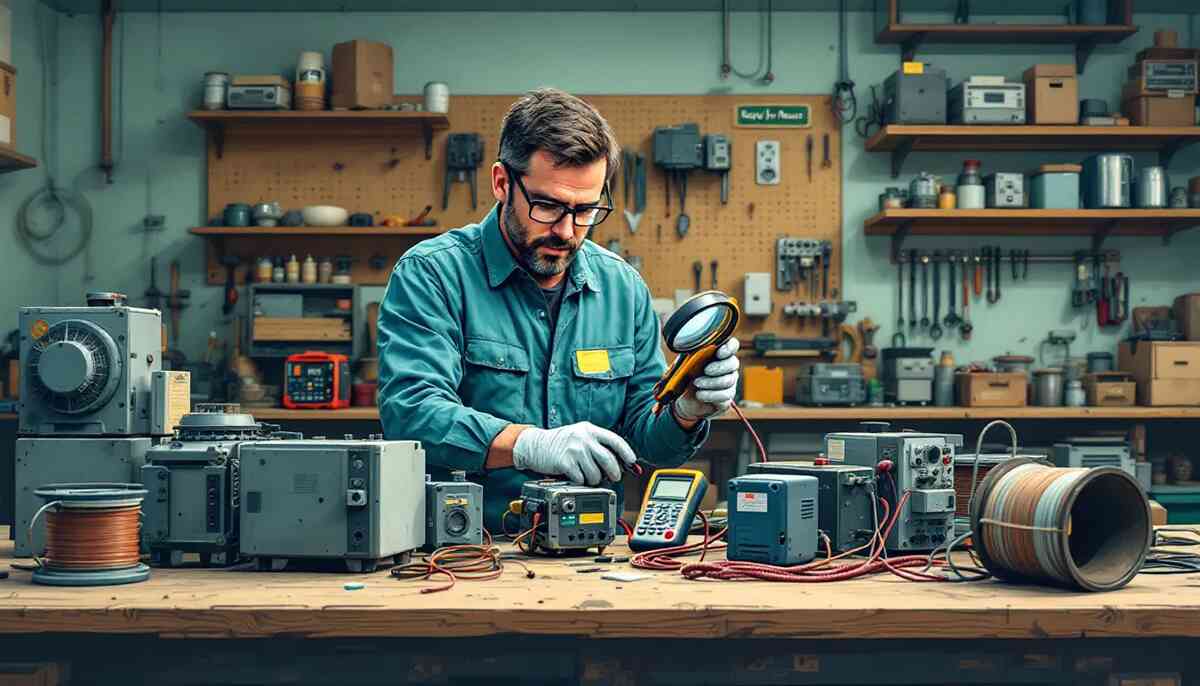
Sustainability and the Bigger Picture
Reusing electrical components isn’t just about saving money—it’s part of a broader shift toward smarter, more sustainable operations. For industrial professionals under pressure to cut costs and carbon, reuse offers a win-win.
Reuse Supports Environmental Responsibility
Every time you reuse a component, you:
- Reduce landfill waste from metals, plastics, and insulation
- Lower the demand for raw material mining and manufacturing
- Cut energy consumption from transportation and packaging
Fact: The EPA estimates that reusing industrial electrical equipment reduces the carbon footprint by up to 60–75% compared to manufacturing new components.
This matters not just to regulators, but to your clients, your board, and your future bids—especially as ESG (Environmental, Social, Governance) goals become part of supplier evaluations.
A Key Part of Circular Economy Practices
The circular economy is built on three pillars:
- Reduce
- Reuse
- Recycle
Reusing tested components—rather than defaulting to disposal—is a tangible, measurable way to contribute to sustainability goals without major operational changes.
- No need to overhaul your facility layout
- No expensive certifications required
- Just smarter asset management
Case Study Insight: A manufacturing plant reduced annual equipment disposal by 27% by integrating reuse tracking into their CMMS, improving both ESG scores and maintenance cost KPIs.
Operational and Financial ROI
Reuse aligns perfectly with lean operations. It reduces:
- Emergency procurement
- Inventory bloat
- Long lead-time exposure
- Project overages tied to part delays
And the savings don’t stop at the parts themselves:
- Less unplanned downtime
- Fewer overnight freight charges
- Lower carbon emissions per work order
It also creates a more agile team—one that can make reuse/replacement decisions quickly, based on process rather than guesswork.
Your Competitive Advantage
Facilities and contractors who adopt smart reuse practices now will:
- Be ahead of future regulatory pushes for waste reduction
- Look stronger on ESG reports and vendor scorecards
- Be able to demonstrate leadership in reliability and sustainability
Pro Tip: Highlight your reuse policy in client RFPs or facility reports—it shows you’re forward-thinking, efficient, and environmentally conscious.
It’s about getting more out of what you already have, without cutting corners. It’s about building systems that are smarter, more resilient, and more sustainable—one inspected component at a time.
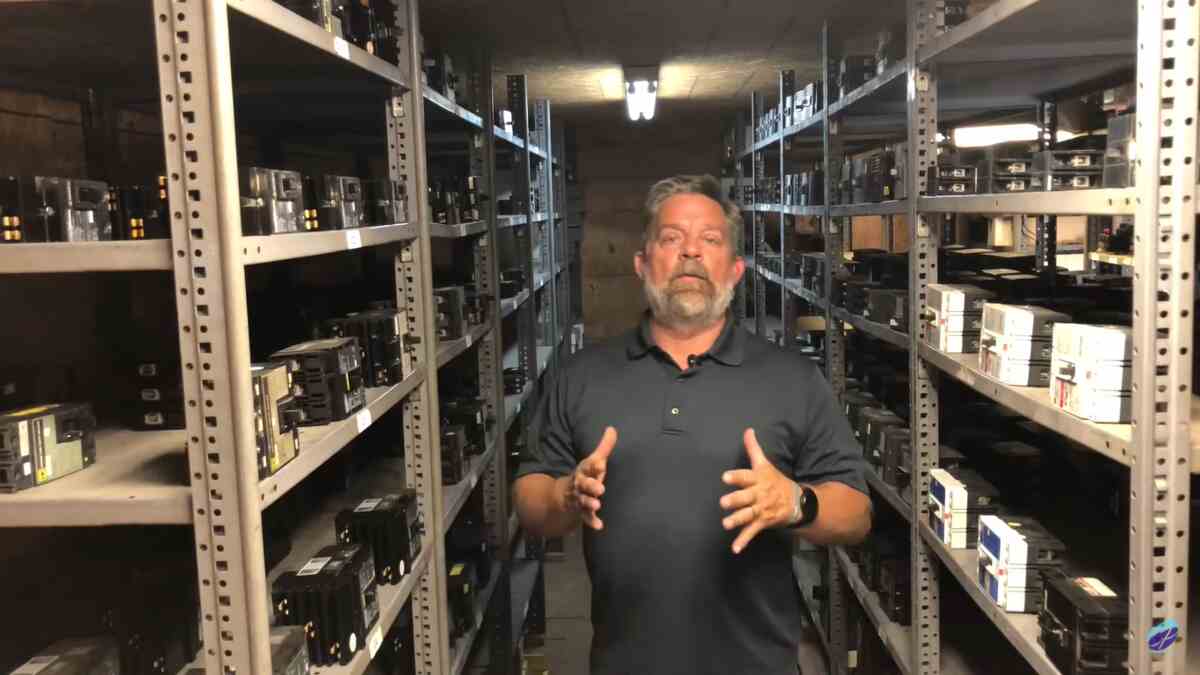
Conclusion
When managed properly, reusing industrial electrical components can be one of the smartest moves you make—financially, operationally, and environmentally.
You’ve now seen:
- The top components that can (usually) be reused safely
- The evaluation steps to inspect and test them properly
- The clear do-not-reuse list to keep your team and systems protected
- The processes and protocols to implement reuse consistently
- The broader benefits to sustainability and operational efficiency
Whether you’re maintaining a facility, managing field crews, or engineering complex automation systems, strategic reuse puts control back in your hands—helping you minimize delays, reduce waste, and extend the life of your equipment responsibly.
If you need help with electrical components reuse or want to sell your old industrial electrical components, contact Electrical Power and Control today at (205) 812-5402.
We’re here to support your success—with dependable insights, tested solutions, and a deep commitment to keeping your operations running smoothly.