Table of Contents
ToggleAsk upper management what their top company concerns are and production always seems to come up. Let’s face it… Without production, the bottom line begins to decrease dramatically. If you happen to be in the maintenance leadership role, sometimes you can feel caught in the middle between upper management and budget limits, preventing planned outages for repairs.
Then it happens; the unwanted failure. Now, the electrical equipment you have been trying to shut down to repair for months has brought production to a standstill and everyone is looking to you for timely answers. I know your position comes with a certain level of stress, but what if you could decrease that level?
When unwanted downtime occurs, proper planning helps to ensure you are back up and running more quickly. Let’s look at three ways to develop a plan that is proven and somewhat easy on your maintenance budget.
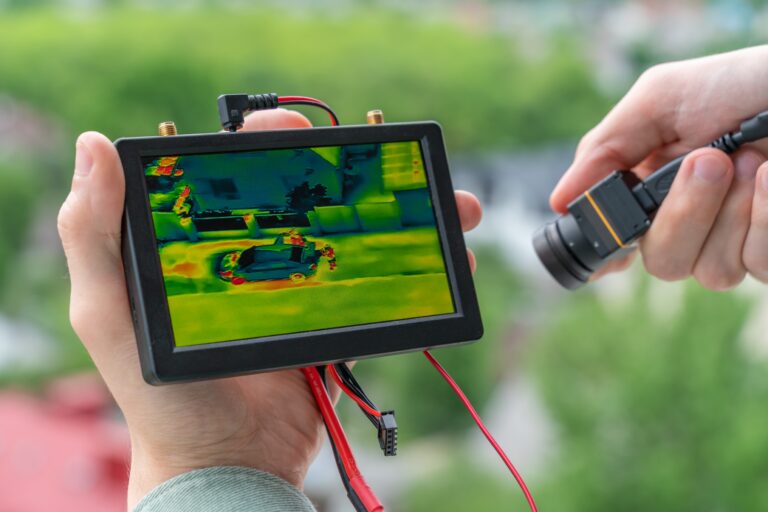
I. THE INFRARED SCAN IS YOUR FRIEND
Picture yourself in a predicament where the need for thorough inspections clashes with the imperative to keep critical equipment running. In these situations, an invaluable asset at your disposal is the infrared scan—a non-intrusive method enabling your maintenance teams to assess the condition of electrical components while they are still operational.
The infrared scan captures images and temperatures of electrical equipment, uncovering discolored connections and hotspots that may indicate potential issues. With modern technology facilitating the storage of scan data on memory cards, you gain a comprehensive record for analysis. This information proves particularly useful when planning scheduled shutdowns for repairs. By identifying potential problems in advance, you can develop a proactive approach, minimizing the risk of unplanned downtime.
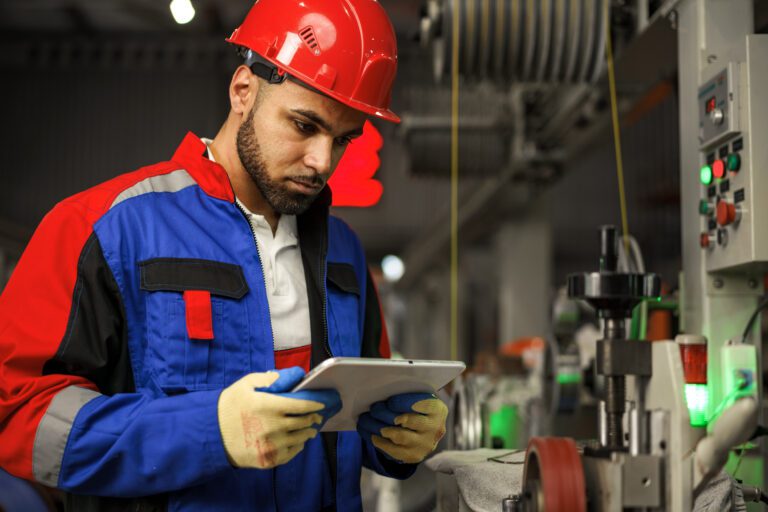
II. ACCURATE INVENTORY IS ESSENTIAL
After you use the infrared scan, as someone in charge of maintenance, you need to sort and understand the data you got. It’s important to have a clear list of the supplies you’ll need to fix things quickly. Make sure you have all the necessary tools, like replacement breaker lugs and contact cleaners, so your maintenance team can use them right away.
For fixing circuit breakers and motor starters, keeping a detailed list is really important. Write down details like catalog numbers, types, and manufacturers. Make sure the replacement circuit breakers are the right size and that thermal overloads fit the motor starters correctly. Doing this carefully not only helps to reduce downtime but also avoids delays from ordering the wrong or unavailable parts.
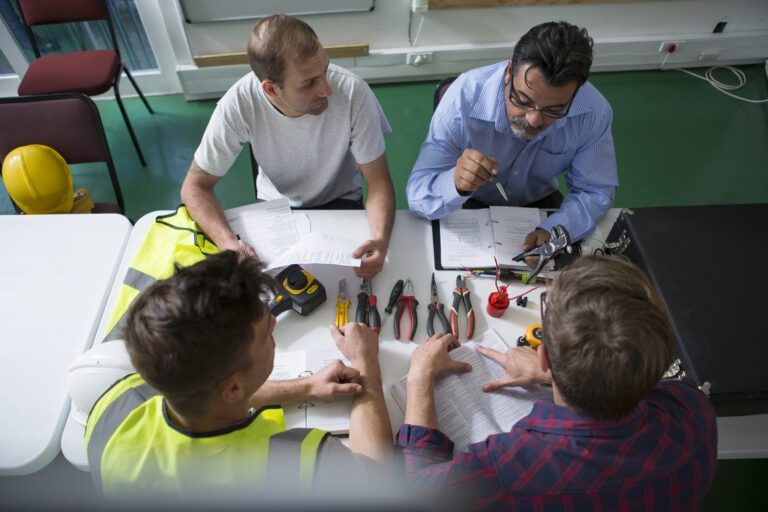
III. INVESTING IN KNOWLEDGE: EMPOWERING MAINTENANCE PERSONNEL
Knowledge is a powerful asset in the field of electrical maintenance. Maintenance leaders should prioritize surrounding themselves with knowledgeable and skilled personnel. As technology evolves, the need for ongoing education becomes paramount. By investing in the training and development of technicians, maintenance leaders build a team that can adapt to changing technologies and emerging challenges.
Educated technicians contribute to a proactive maintenance culture, where potential issues are identified and addressed before they escalate into critical failures. The leader’s peace of mind is significantly enhanced when they know they have a team of capable individuals capable of handling complex maintenance tasks. This approach not only reduces stress levels but also improves the overall efficiency and effectiveness of the maintenance team.
Implementation of Infrared Scans
Let’s take a closer look at the first strategy: utilizing infrared scans for proactive planning. Infrared thermography is a technique that captures the heat emitted by an object and converts it into an image, commonly known as a thermogram. In the realm of electrical maintenance, infrared scans provide valuable insights into the condition of equipment, helping identify potential issues before they lead to unplanned downtime.
To implement infrared scans effectively, maintenance leaders should consider the following steps:
Equipment Selection: Identify critical equipment that cannot be easily shut down for inspection. This might include circuit breakers, motor controls, or other essential electrical components.
Technology Adoption: Invest in infrared cameras or hire professionals equipped with this technology. Modern infrared cameras are user-friendly and provide accurate temperature readings, making it easier for maintenance teams to identify anomalies.
Regular Scanning Routine: Establish a routine for conducting infrared scans. Regular scans can help in creating a baseline for equipment performance and detecting any deviations over time.
Data Documentation: Ensure proper documentation of infrared scan data. Modern infrared cameras often come with memory card storage capabilities. This data can be cataloged and used for comparison in subsequent scans.
Training and Familiarization: Train maintenance personnel on using infrared cameras and interpreting scan results. Familiarity with the technology enhances the team’s ability to identify potential issues accurately.
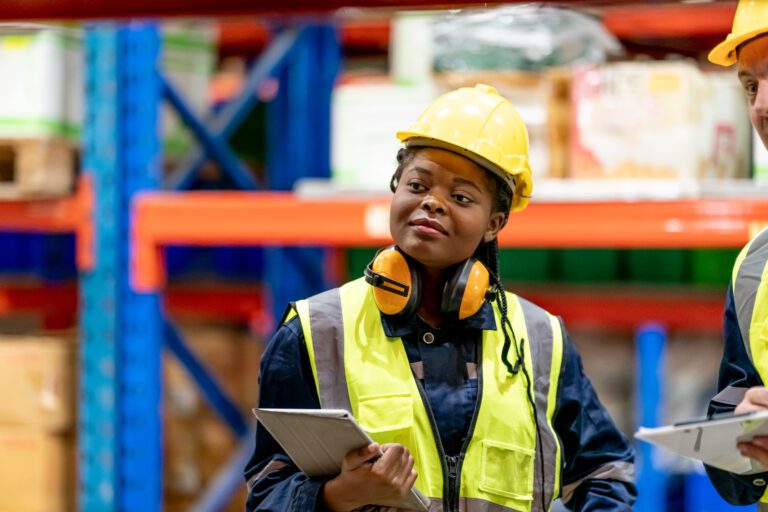
Effective Inventory Management
Moving on to the second strategy, maintaining a well-organized inventory is crucial for swift repairs. An accurate and well-managed inventory ensures that maintenance teams have the necessary tools and replacement parts readily available, minimizing the time required to address equipment failures.
Here are steps to implement effective inventory management:
Cataloging and Categorization: Organize the inventory systematically, categorizing items based on their nature and usage. Create a clear catalog with detailed information about each item, including part numbers, specifications, and quantities.
Regular Audits: Conduct regular audits of the inventory to track usage patterns and identify items that need replenishment. This proactive approach helps in preventing shortages and ensures that the inventory is always well-stocked.
Supplier Relationships: Build strong relationships with reliable suppliers. Ensure open communication channels to facilitate quick orders and deliveries when new supplies are needed.
Emergency Kits: Create emergency kits containing essential tools and commonly used replacement parts. These kits can be easily accessible during urgent repair situations, reducing the time needed to gather necessary items.
Digital Inventory Management Systems: Consider implementing digital inventory management systems. These systems can automate processes, provide real-time updates on inventory levels, and generate alerts when certain items need reordering.
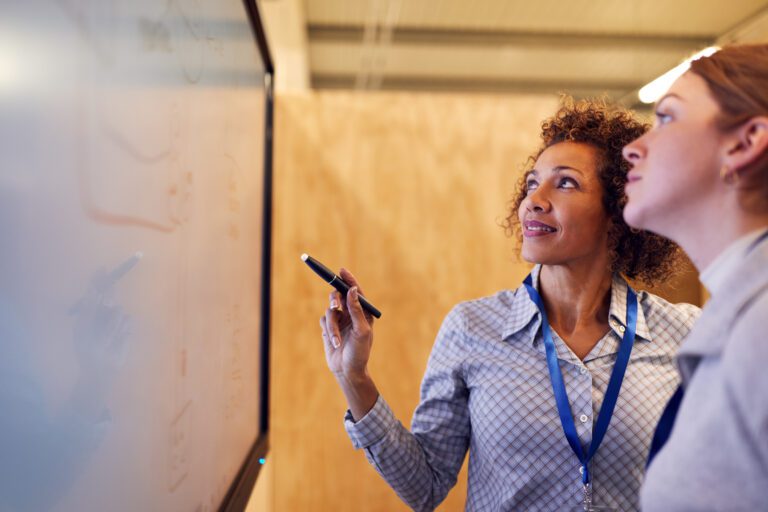
Investing in Knowledge
Lastly, let’s explore the third strategy: investing in the knowledge of maintenance personnel. Having a team of well-trained and knowledgeable technicians is fundamental to the success of any maintenance operation. As technology evolves and equipment becomes more sophisticated, continuous education becomes essential to keep the team updated and capable of handling diverse challenges.
Here’s how maintenance leaders can invest in the knowledge of their personnel:
Training Programs: Establish regular training programs to update technicians on the latest technologies and maintenance practices. This could include workshops, online courses, or hands-on training sessions.
Certifications: Encourage technicians to pursue relevant certifications in their field. Certifications validate their expertise and provide a structured learning path.
Knowledge Sharing: Foster a culture of knowledge sharing within the team. Experienced techni cians can mentor newer team members, creating a collaborative environment where skills are passed down.
Stay Informed about Industry Trends: As a leader, stay informed about industry trends and emerging technologies. This knowledge can guide training programs and help the team stay ahead of potential challenges.
Regular Skill Assessments: Conduct regular skill assessments to identify areas where individual technicians may need additional training or support. This ensures a well-rounded and capable team.
I know that stress will always be part of the job, but knowing that we can take simple steps to proper planning, accurate inventory, and education, we can reduce the level and, hopefully, the effect that stress can have on each of us.